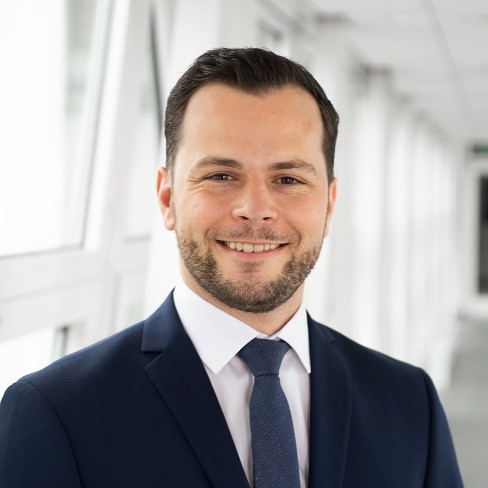
The mobility and energy transition brings along new challenges for the finishing of gears and profiles. As part of the “Trust in Technology” campaign, KAPP NILES has already presented innovative solutions for electromobility. From 2025 onwards, attention will now be increasingly focused on wind power applications.
“As a leading manufacturer in gear technology, we at KAPP NILES are proud to support the development of the wind power industry. Our solutions help to increase the efficiency and lifespan of wind turbines and to promote the expansion of renewable energies. KAPP NILES is determined to make a positive impact on a sustainable energy future with the highest precision and responsibility. That is why we are increasingly focusing on our expertise and technologies in the machining of gears in wind turbines,” said Matthias Kapp, Managing Director at KAPP NILES.
Roughly 80% of wind turbines are designed with a gear box translating the rotational energy of the rotor blades for the generator. In this context, planetary gearboxes with multiply stages are very common. Due to the growing power output of modern wind turbines these gearboxes and the gears within are increasing in size and belong to the most stressed components with correspondingly high demands โ both in terms of quality and productivity.
For almost three decades, KAPP NILES has been offering tailor-made products and technologies for the finishing of wind turbine gears. The relevant gears in a modern wind turbine include the planetary gears, the sun gears and the ring gears of the gearbox as well as the pinions of the yaw and pitch drives. With solutions from KAPP NILES, these can be ground and measured with high precision.
Complete solutions from a single source Profile grinding machines of the KNG master series are well suited for grinding the planetary gears for wind turbine gearboxes with tip diameters up to 1,250 mm. ZP series machines are ideal for grinding gears with even larger tip diameters and modules to combine maximum productivity with highest machining qualities, the ZP series can be equipped with an automatic tool changer. This solution provides the possibility to execute several different grinding operations with minimal set-up and non-productive times.
Sun gears can also be ground on machines of the ZPseries. As these gears are usually on a shaft, the function for wobble determination can be used to automatically compensate for clamping errors, further reducing set-up times.
The ZPI profile grinding machine is suitable for grinding the internal ring gears in planetary gearboxes with large modules and an outer diameter of up to 5,000 mm. Using 5-axisโinterpolation even large modifications can be productively ground almost twist-free by means of double-flank grinding. Thanks to machine-integrated simulation, the expected grinding results can be evaluated and optimised in advance.
The KNG master series is also ideal for machining jaw and pitch drive pinions. The high performance of the grinding spindle and the double spindle dressing unit contribute to excellent grinding results to be achieved with maximum productivity. The user-friendly and intuitive data entry promotes an easy generation of complex modifications.
In addition, customers can benefit from KAPP NILES solutions when measuring wind turbine gears. Planetary gears, for example, can be measured on the KNM 9X measuring machine, which is suitable for components with a diameter of up to 1,250 mm and a workpiece weight of up to 1,500 kg. Air bearings and linear motors ensure high-precision and fast measurement. Especially for large components, the movable counter support and the mobile control panel contribute to easy loading and ergonomic operation.
Larger external gears and ring gears in wind turbine gearboxes with a workpiece diameter of up to 5,000 mm can be measured on the largest KNM X series supporting a maximum table load of 40,000 kg.
In addition to the grinding and measuring machines, the quality of the dressing tools is particularly crucial to achieve the best results in demanding grinding tasks. This is why KAPP NILES offers diamondโform rolls with wear-resistant CVD inserts to achieve precise geometries and the highest surface qualities in profile grinding applications.
In the development of KAPP NILES grinding and measuring machines, we can draw on many decades of experience. In combination with innovative ideas, state-of-the-art machine concepts are created and built in excellent manufacturing quality for maximum accuracy and process stability.
“We are convinced that an excellent result for our customers can only be achieved if machine, tool, technology and measuring technology are optimally coordinated. As a system supplier, KAPP NILES therefore offers complete precision solutions for the wind power industry,” says Matthias Kapp.
About KAPP NILES
KAPP NILES is a globally operating group of companies with high-quality and economical solutions for finishing gears and profiles and is partner for companies from numerous industrial sectors in the mobility, automation and energy segments. The perfect interaction between machine, tool, technology and metrology enables extremely precise machining to a thousandth millimetre.
Press contact:
Anuschka Friedrich | Communication / Marketing
Phone: + 49 9561 866-1253
Email: anuschka.friedrich@kapp-niles.com
KAPP GmbH & Co. KG | 96450 Coburg | Callenberger Str. 52