2024 Emerging Tech Webinar Series
July 10, 2024
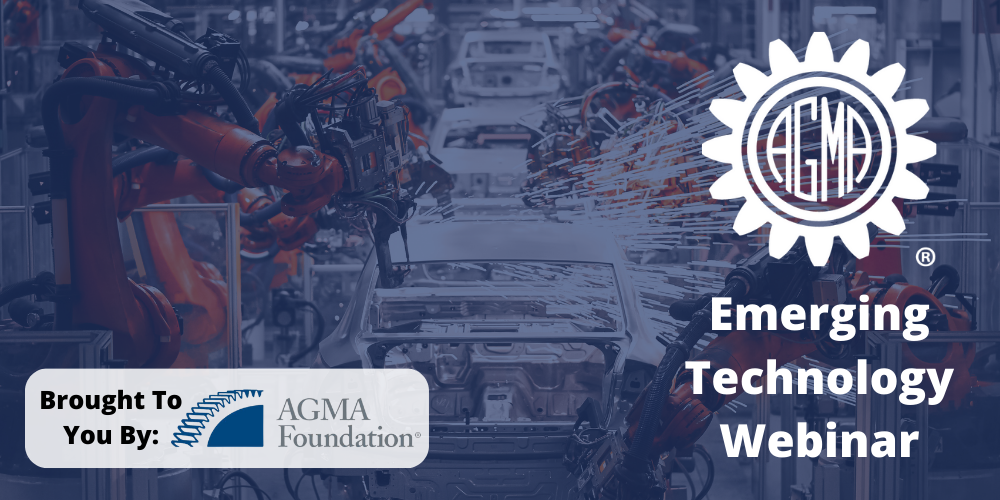
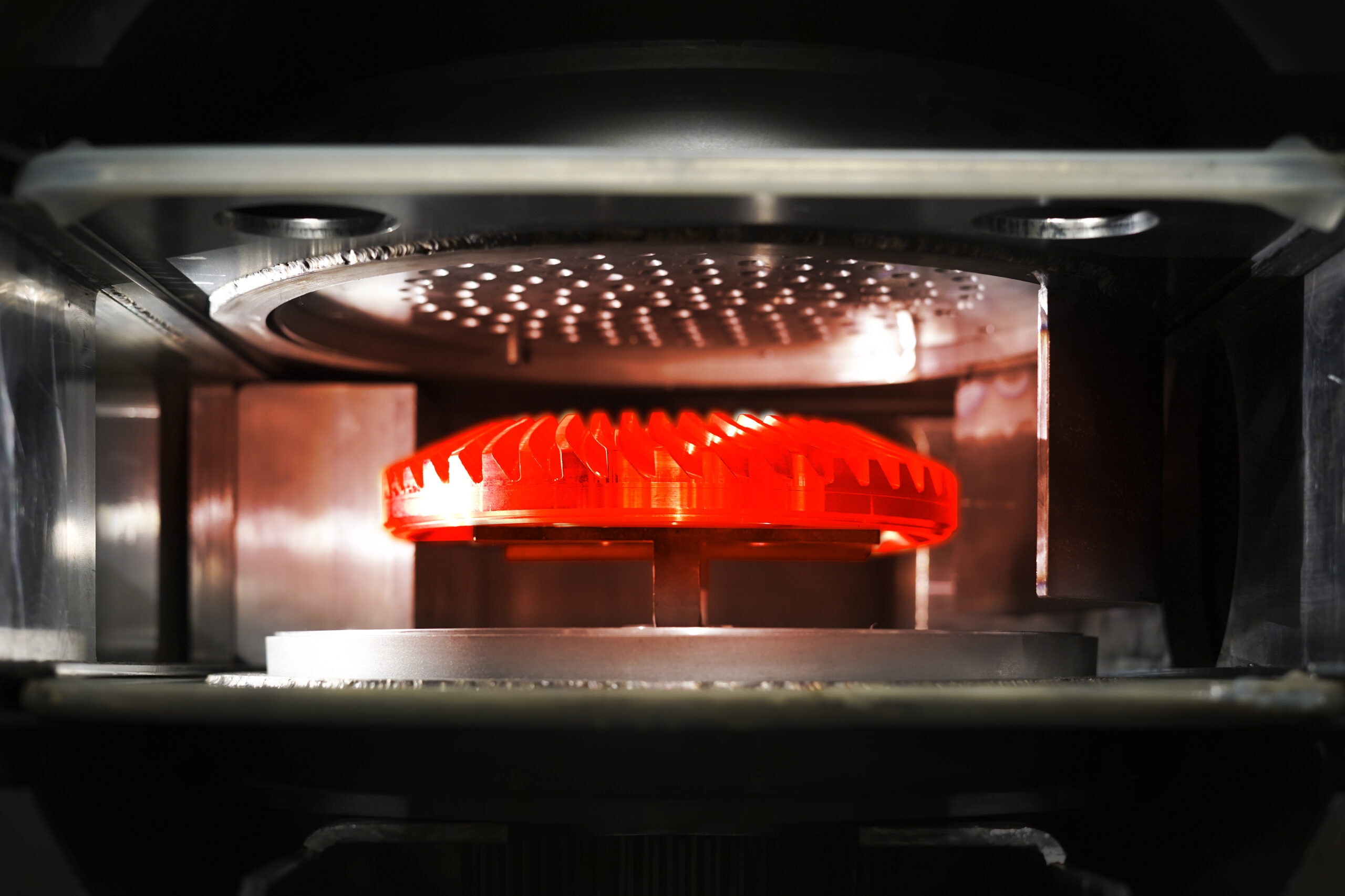
It is well known that distortion has and continues to present a challenge to the heat treater when hardening/carburizing gears. However, recent advances in quenching technology are improving the opportunity for improved distortion control. 4 Dimension High-Pressure Gas Quenching (4DQ) is a unique gas quenching process that uses both a special quenching chamber design with part rotation to minimize distortion during the quenching process. 4DQ gives one the ability to โengineerโ the quenching process by controlling quench pressure, gas velocity, gas manifold design, table rotation, table oscillation, and time-dependent gas flow. The system’s flexibility allows users to customize the quenching process for reduced distortion, providing repeatability and precise accuracy in their heat treatment.
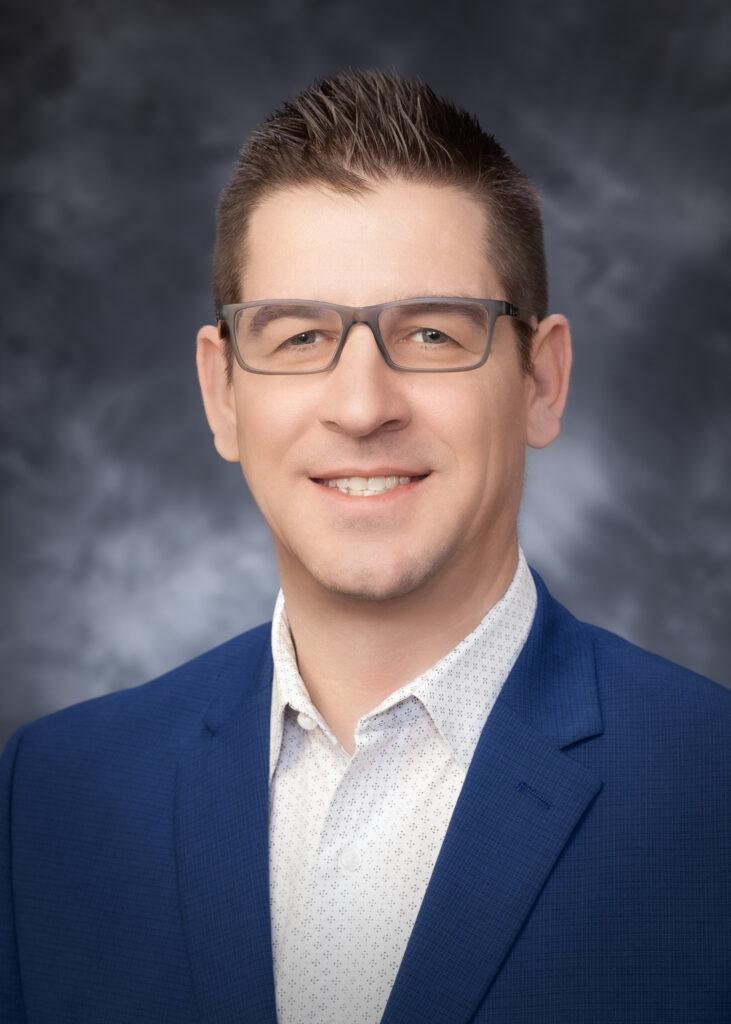
Tom Hart
Product Manager โ Vacuum Furnaces, SECO/VACUUM Technologies
Tom is a Product Manager specializing in Vacuum Furnaces with SECO/VACUUM Technologies and has been in precision manufacturing and heat treatment industries for 20 years.
In his role, Tom collaborates closely with partners, providing support for heat treatment processes, equipment, and infrastructure specific to vacuum furnaces. His experience spans various heat treatment techniques, including hardening, annealing, low-pressure carburizing, tempering, sintering, vacuum brazing, and more.
Tom had experience in furnace designs for aerospace, power generation, tool & die, medical, machine building, automotive, and commercial heat treatment markets. He is also an active member in groups such as American Gear and Manufacturing Association, ASM International, Gear Research Institute (Aerospace Bloc) & Material Treating Institute.
.
Please fill out the form below to access the webinar.